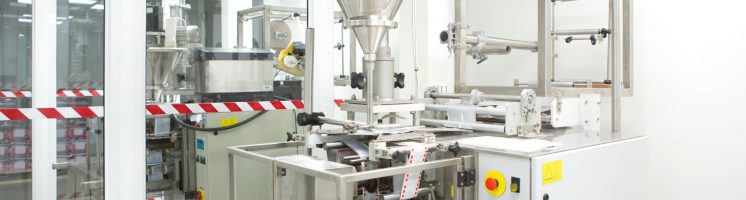
Desvendando a Qualificação de Equipamentos: Uma Jornada de Precisão e Conformidade
Categoria: Artigo, Blog, qualificação
Entendendo a Essência da Qualificação de Equipamentos
No cenário atual das indústrias, onde a precisão e a eficiência são cruciais, a qualificação de equipamentos se destaca como uma prática essencial. Ela representa mais do que um simples procedimento; é a garantia de que cada equipamento usado nos processos de produção opera não apenas de acordo com as especificações técnicas, mas também em conformidade com os rigorosos padrões de qualidade e segurança. Neste cenário, entender a qualificação de equipamentos é entender o coração dos processos industriais modernos.
Em indústrias regulamentadas como as farmacêuticas,
cosméticas e alimentícias, a qualificação de equipamentos transcende a mera
adequação às normas. Ela se torna parte integrante da cultura de qualidade,
assegurando que cada produto fabricado atenda aos mais altos padrões de
qualidade e eficácia. Com a crescente complexidade dos processos de fabricação
e a constante evolução das normativas, a qualificação de equipamentos surge não
apenas como um requisito legal, mas como uma necessidade estratégica para
manter a competitividade e a reputação no mercado global.
O que é Qualificação de Equipamentos?
A qualificação de equipamentos é um conceito fundamental na indústria moderna, especialmente em setores onde a precisão e a confiabilidade são imperativas. Mas o que realmente significa qualificar um equipamento? Em sua essência, a qualificação de equipamentos é um processo sistemático que verifica e valida que todo equipamento industrial está instalado corretamente, funciona adequadamente e é capaz de produzir consistentemente os resultados desejados. Este processo não é apenas uma etapa única; é um ciclo contínuo que envolve várias fases de avaliação e ajustes ao longo da vida útil do equipamento.
Esta prática é particularmente crítica em indústrias como a farmacêutica, biotecnologia, alimentícia e química, onde os equipamentos desempenham um papel vital na garantia da qualidade do produto final. Aqui, a qualificação de equipamentos vai além de simplesmente cumprir as regulamentações. Ela se torna um pilar para garantir a eficácia, segurança e integridade dos produtos. Cada peça de equipamento, seja uma simples balança de laboratório ou uma complexa linha de produção automatizada, deve passar por uma rigorosa avaliação para assegurar que atende às especificações necessárias para a sua função. A qualificação de equipamentos, portanto, é um elemento crítico que sustenta a confiança na integridade dos processos e na qualidade dos produtos finais.
A Importância Vital da Calibração na
Qualificação de Equipamentos
No processo de qualificação de equipamentos, a calibração emerge como um passo crucial, essencial para garantir a precisão e a confiabilidade dos resultados de produção. Mas por que a calibração é tão importante? A calibração envolve a comparação das leituras de um equipamento com um padrão conhecido e aceito, ajustando-o conforme necessário para garantir que ele forneça leituras precisas. Em indústrias onde a exatidão é fundamental, como as farmacêuticas e biotecnológicas, uma calibração inadequada pode levar a erros significativos, afetando a qualidade do produto e, por extensão, a segurança do consumidor.
Esta etapa não é apenas uma formalidade; é uma necessidade imperativa para manter a integridade do processo de fabricação. Por exemplo, em um ambiente de produção farmacêutica, a calibração inadequada de um equipamento de medição pode resultar em dosagens incorretas de ingredientes ativos, comprometendo a eficácia do medicamento produzido. Da mesma forma, na indústria alimentícia, uma calibração imprecisa pode afetar a consistência e a qualidade dos alimentos produzidos. Assim, a calibração torna-se um elemento chave para garantir que os processos de produção não apenas atendam aos padrões de qualidade, mas também cumpram com as regulamentações de segurança rigorosas impostas por órgãos reguladores. Em resumo, a calibração é o alicerce sobre o qual a confiança e a conformidade na qualificação de equipamentos são construídas.
Entendendo os Tipos de Qualificação de Equipamentos
A qualificação de equipamentos é um conceito multifacetado, compreendendo diferentes tipos que se encaixam em várias fases do ciclo de vida de um equipamento. Cada tipo de qualificação tem um papel distinto, garantindo que os equipamentos não apenas estejam instalados corretamente, mas também operem de forma eficiente e produzam resultados consistentes. Vamos explorar os principais tipos:
Qualificação de Instalação (QI)
A Qualificação de Instalação é o primeiro passo no processo de qualificação. Ela verifica se o equipamento foi instalado corretamente e de acordo com as especificações do fabricante. Este passo inclui a verificação de todos os aspectos físicos e técnicos do equipamento, como conexões elétricas, tubulações, software e configurações ambientais. A QI assegura que o equipamento esteja adequadamente posicionado e configurado para funcionar como esperado, estabelecendo uma base sólida para as operações subsequentes.
Qualificação de Operação (QO)
Seguindo a QI, a Qualificação de Operação testa se o equipamento opera dentro dos parâmetros esperados em todas as condições planejadas. Este passo envolve testes rigorosos para verificar se todas as funções do equipamento estão operando conforme especificado. A QO é crucial para confirmar que o equipamento não só foi instalado corretamente, mas também é capaz de realizar as tarefas para as quais foi projetado, sob várias condições e configurações.
Qualificação de Desempenho (QD)
A Qualificação de Desempenho é a etapa final, onde o equipamento é testado em condições reais de operação para garantir que ele produza resultados consistentes e confiáveis. Este processo envolve a execução de testes prolongados para validar a performance do equipamento sob uso normal. A QD é essencial para demonstrar que o equipamento não só funciona tecnicamente, mas também atende aos requisitos de desempenho e qualidade necessários para a produção segura e eficaz.
Entendendo FAT e SAT no Contexto da Qualificação de Equipamentos
Dentro do amplo espectro da qualificação de equipamentos, dois termos se destacam por sua importância: o Teste de Aceitação na Fábrica (FAT) e o Teste de Aceitação no Local (SAT). Esses testes são etapas cruciais que garantem a conformidade e a eficiência dos equipamentos antes e após sua instalação.
Teste de Aceitação na Fábrica (FAT)
O FAT é um processo proativo e preventivo realizado na fábrica do fornecedor antes do envio do equipamento. Esta etapa envolve uma série de testes detalhados para verificar se o equipamento atende a todas as especificações contratadas e se está pronto para ser instalado. Durante o FAT, os técnicos e engenheiros realizam uma bateria de testes para assegurar que o equipamento funcione corretamente em um ambiente controlado, identificando e corrigindo quaisquer problemas antes da entrega. Este processo não apenas economiza tempo e recursos, evitando retrabalho no local do cliente, mas também garante que o equipamento chegue pronto para ser integrado ao processo de produção com o mínimo de interrupções.
Teste de Aceitação no Local (SAT)
Após o equipamento ser entregue e instalado no local do usuário final, é realizado o SAT. Este teste é essencial para verificar se o equipamento mantém sua funcionalidade e conformidade em um novo ambiente, que pode ter variáveis diferentes do ambiente da fábrica do fabricante. O SAT inclui a verificação de que o equipamento foi instalado corretamente e está operando conforme esperado no contexto específico de sua utilização final. Este teste é crucial para assegurar que o equipamento não só foi bem fabricado, mas também está adequadamente integrado aos processos e sistemas existentes no local de instalação.
Tanto o FAT quanto o SAT são componentes integrais do processo de qualificação de equipamentos, oferecendo uma dupla camada de garantia: primeiro no ambiente do fabricante e depois no ambiente operacional real. Eles são fundamentais para assegurar a qualidade, a eficiência e, sobretudo, a segurança dos equipamentos industriais.
Cada uma dessas etapas de qualificação desempenha um papel vital na garantia de que os equipamentos utilizados nas indústrias cumpram com os rigorosos padrões de qualidade e segurança, fundamentais para a integridade do processo de fabricação e a confiança dos consumidores nos produtos finais.
Para ilustrar a importância e a aplicabilidade da qualificação de equipamentos, vamos considerar um exemplo prático no contexto de uma indústria farmacêutica. Imagine uma linha de produção onde uma nova máquina de encapsulamento será introduzida. Esta máquina é essencial para garantir a dosagem precisa dos medicamentos e a eficiência do processo de produção. O processo de qualificação começa com a Qualificação de Instalação (QI), onde a equipe verifica se a máquina foi instalada corretamente, com todas as suas conexões elétricas, mecânicas e de software conforme as especificações do fabricante. Isso inclui a checagem de todos os componentes, desde sensores até software de controle.
Após a instalação, segue-se a Qualificação de Operação (QO). Aqui, a máquina é testada em diferentes modos de operação para garantir que todas as suas funções estejam operando conforme o esperado. Isso pode incluir testes de velocidade, precisão de enchimento e confiabilidade em várias condições de operação. Uma vez que a QO é concluída com sucesso, a máquina passa pela Qualificação de Desempenho (QD), onde é operada em condições reais de produção. Durante a QD, a máquina de encapsulamento é usada para produzir lotes de teste, e os resultados são cuidadosamente analisados para assegurar que a máquina produza cápsulas com a dosagem correta, consistência e qualidade.
Profissionais e Formação em Qualificação de Equipamentos
A qualificação de equipamentos é uma tarefa que exige não apenas conhecimento técnico, mas também uma compreensão aprofundada dos processos industriais e normas regulatórias. O sucesso deste processo depende em grande parte dos profissionais envolvidos, que devem possuir uma combinação de experiência prática e formação teórica. Engenheiros, técnicos e especialistas em qualidade são peças-chave nesta operação, cada um trazendo habilidades e conhecimentos específicos para garantir que o equipamento seja qualificado de maneira eficiente e eficaz.
Esses profissionais são responsáveis por planejar e executar as diferentes fases da qualificação, desde a instalação até a operação e o desempenho dos equipamentos. Eles devem estar familiarizados com os padrões e regulamentos da indústria relevantes, além de possuírem habilidades analíticas e de resolução de problemas para identificar e corrigir quaisquer desvios ou falhas durante o processo. Para manter-se atualizados com as tecnologias em constante evolução e os padrões regulatórios, é crucial que esses profissionais participem de cursos de formação contínua e desenvolvimento profissional. Estes cursos podem abranger desde workshops específicos sobre novas tecnologias de equipamentos até programas de certificação em normas de qualidade e regulamentos da indústria.
Além disso, a troca de experiências e melhores práticas entre profissionais de diferentes setores é um aspecto vital para o contínuo aprimoramento no campo da qualificação de equipamentos. Ao investir no desenvolvimento destes profissionais, as indústrias não apenas asseguram a conformidade e a eficiência dos seus processos, mas também fomentam uma cultura de qualidade e inovação contínua.
Reforçando a Indispensabilidade da Qualificação de Equipamentos
À medida que chegamos ao final de nossa exploração sobre a qualificação de equipamentos, torna-se evidente que este processo é muito mais do que uma mera formalidade regulatória; é uma pedra angular na garantia da qualidade e eficiência na produção industrial moderna. A qualificação de equipamentos não é apenas uma etapa necessária para cumprir com as normas regulamentares, mas também uma estratégia empresarial inteligente que assegura a produção de produtos seguros, eficazes e de alta qualidade. Em indústrias onde a precisão e a confiabilidade são fundamentais, como nas áreas farmacêutica, alimentícia e cosmética, a qualificação de equipamentos é um elemento essencial para manter a integridade do processo de fabricação e a confiança dos consumidores nos produtos finais.
Este processo meticuloso, que envolve a calibração, a instalação, a operação e o desempenho dos equipamentos, reflete o compromisso da indústria com a excelência e a melhoria contínua. Além disso, destaca a importância dos profissionais qualificados, cujo conhecimento e dedicação são fundamentais para a implementação bem-sucedida da qualificação de equipamentos. Ao investir na qualificação adequada de equipamentos, as empresas não só cumprem com as exigências regulatórias, mas também fortalecem sua posição no mercado, melhorando a eficiência de seus processos e a qualidade de seus produtos. Em última análise, a qualificação de equipamentos é um investimento valioso na sustentabilidade e no sucesso a longo prazo de qualquer empresa que dependa de processos de fabricação robustos e confiáveis.