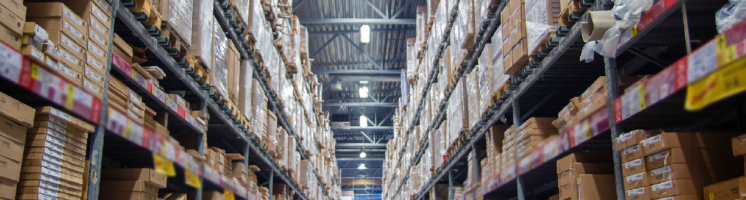
Fique atento a esse assunto ! Mapeamento térmico de depósitos
Categoria: Artigo, Blog, mapeamento térmico, qualificação, validação
O mapeamento térmico de depósitos é um estudo que a cada dia vem sendo procurado por profissionais que atuam em indústrias farmacêuticas e vem sendo cobrado pelos órgãos regulatórios ( Covisa , Visa e Anvisa ).
Com a condição climática do país mudando a cada ano é de extrema importância realizar esse estudo anualmente para avaliar se os pontos críticos de temperatura ( região mais fria e região mais quente ) não se alteraram .
Com a revisão da USP 36 , capítulo 1079 , houve uma alteração de período de estudo . Antes era indicado realizar o estudo por no mínimo 72 horas , agora alterou-se esse período para no mínimo 7 dias de monitoramento .
Fique atento a esse assunto !
Como todos sabem o mapeamento térmico é um item fundamental, quando falamos em Boas Práticas de Armazenagem para depósitos climatizados e não climatizados.
No entanto, temos algumas perguntas frequentes quando falamos neste tema, como:
- Faço os testes de quanto em quanto tempo?
- Quanto tempo deve-se realizar as medições?
- Como definir a quantidade de sensores?
- Onde localizar estes sensores?
- Quais instrumentos utilizar?
- Qual a frequência de aquisição dos dados?
O presente artigo serve como referência documentada para definir os passos para um correto mapeamento térmico, de forma documentada e estruturada.
Para a realização do Mapeamento, necessitamos passar por alguns itens fundamentais para execução dos trabalhos. Estes itens estão descritos abaixo:
- Planejamento
- Documentação
- Execução
- Análise dos Resultados e Relatório final
- Mantendo o status de Validado
Planejamento
O planejamento é um dos itens fundamentais para execução do trabalho de mapeamento térmico.
O planejamento pode ser divido nas seguintes etapas:
- Pré-Requisitos;
- Análise de Riscos ;
- Seleção da Tecnologia adequada para Mapeamento;
- Quantidade de Sensores.
Pré-Requisitos
Antes iniciar as etapas do mapeamento devemos verificar alguns pré-requisitos são atendidos, tais como:
- Conclusão da Qualificação de Instalação e Operação do Sistema de HVAC do Almoxarifado (para Almoxarifados Climatizados);
- A área esta acabada e com todos os seus componentes (tais como porta pallets, Portas, Luminárias, etc)
- Se todos os desenhos estão atualizados. Este item auxilia na documentação para descrever as localizações dos pontos
Análise de Riscos
Deve ser feita uma avaliação de riscos para verificar itens relacionados ao almoxarifado.
A ferramenta a ser utilizada é de livre escolha do responsável dos testes. Segue alguns exemplos:
- FMEA
- QRM 5 do GAMP
- FMECA
- Arvore de falhas
- Espinha de peixe
- HACCP
- HAZOP
Na avaliação de riscos devem ser considerados os seguintes itens:
Sazonalidade dos testes – Definir em qual ou quais estações do ano devem ser feitos os testes (Verão, Inverno, Outono ou Primavera). É recomendável fazer no inverno e verão;
Frequência e tempo de medição – definir de quanto em quanto tempo deve ser realizada as medições do estudo (como referencia para depósitos onde não há uma mudança brusca de temperatura e umidade o tempo de 15 minutos é aceitável. Em casos onde tenhamos equipamentos com mudanças buscas de temperatura, como por exemplo, validação de transporte ou salas climatizadas, este tempo deve ser de no máximo 5 minutos).
O estudo deve ser feito por um período de 7 dias (1 semana) para os estudos com carga e sem carga.
Identificação de áreas de Risco – As áreas de riscos devem ser levadas em consideração avaliando os seguintes aspectos:
- Volume do espaço – Um grande armazém ou depósito tem encargos de controle diferentes do que uma área GAMPde armazenamento pequena, com maiores exigências no sistema HVAC e o potencial para uma maior variação de temperatura e umidade em vários locais.
- Capacidade Interna – A capacidade dos difusores ou ventiladores para circular o ar adequadamente.
- Diferenças de temperaturas – Gradientes de temperatura entre o piso mais frio e o ar mais quente perto do teto.
- Fontes externas – Fontes de energia independentes, tais como aquecedores de espaço, ar condicionados e ventiladores, os quais criam bolsões quentes ou frios.
- Montagem dos Racks – Layout de racks, prateleiras e paletes que obstruem o fluxo de ar.
- Posicionamento dos sensores – Localização de sensores de controle HVAC. Por exemplo, um termostato localizado perto de uma fonte de calor ou frio pode fazer com que a temperatura do espaço flutue excessivamente.
- Locais Criticos – Locais perto de fontes de calor ou frio, tais como telhado e paredes exteriores, janelas, e docas de carregamento.
- Locais de Tráfego intenso – Áreas de tráfego intenso, onde o produto ou equipamento é movido.
Definição das Variáveis – Deve-se definir quais variáveis deverão ser medidas (temperatura somente ou temperatura e umidade). Esta definição deve tomar como base a criticidade dos produtos armazenados.
Seleção da Tecnologia adequada para Mapeamento
Atualmente existem vários tipos de tecnologias para a realização do mapeamento térmico como:
- Dataloggers
- Validadores
Para o mapeamento térmico devido a facilidade e ao custo, normalmente é utilizado o Datalogger.
O sistema Datalogger consiste na programação de loggers, através de um software de interface entre o computador e o logger.
Independente da marca ou modelo do logger a ser utilizado, deve sempre se atentar se o mesmo está calibrado e validado conforme o guia da validação de sistemas computadorizados da Anvisa ou de acordo com a norma 21 CFR Part 11 do FDA.
Quantidade de Sensores
Não existem uma quantidade correta de sensores mínimos e máximos para o mapeamento térmico.
O que temos que nos atentar é que todos os pontos críticos definidos na análise de riscos foram considerados. Outra forma de abranger o depósito como um todos é avaliar o mesmo em pelo menos 3 níveis, sendo o primeiro na altura da posição de pallet mais baixo, o segundo na metade e o terceiro na posição de pallet mais alto (vide exemplo abaixo)
Já no sentido longitudinal, pode-se adotar por exemplo, uma distância padrão (+/- 7 metros) e avaliar os 3 níveis (vide figura abaixo).
Deve-se lembrar que esta distância varia de depósito a depósito.
E aconselhável inserir sensores do lado externo do prédio para verificar temperatura e umidade ambiente e próximo à portas de entrada e saída do depósito.
Documentação
Após a etapa de planejamento, o próximo passo é colocar no papel todas as rotinas de testes, como:
- Posicionamento e quantidade de sensores (se possível inserir desenhos, layouts, etc);
- Quantos sensores podem falhar durante o teste (normalmente se coloca o valor de 10% );
- Critérios de aceitação para as variáveis selecionadas (temperatura e umidade);
- Cálculos estatísticos: Máximo, mínimo, média e MKT (TCM)
- Quais cargas estamos realizando os testes
Obs: para a qualificação inicial, fazer 2 testes, um com carga vazia e outra com carga cheia do depósito. Para revalidações, fazer os testes com a carga habiltual do depósito. Durante os testes, o depósito deve ser utilizado normalmente.
O nome deste documento é protocolo de qualificação de desempenho, mas em algumas empresas este nome pode mudar, como: protocolo de mapeamento térmico, protocolo de revalidação térmica de depósito etc.
Independente dos nomes adotados deve haver um roteiro de testes para a execução dos trabalhos.
Execução
Com o protocolo ou roteiro de testes na mão, a execução consiste em programar os loggers e distribuir nos locais determinados na análise de riscos e protocolo de qualificação.
Um ponto muito importante é colocar os loggers sempre em locais seguros, longe de impactos com as empilhadeiras e contato direto com água (para sensores ambientes externos).
Análise dos Resultados e Relatório final
Após o estudo realizado, deve-se analisar os dados e elaborar o relatório final.
A análise dos dados consiste em verificar os seguintes fatores:
- Identificação dos pontos mais quentes e mais frios;
- Caso algum ponto saia de especificação, verificar por quanto tempo o mesmo ficou fora;
- Verificar a média de cada ponto de medição;
- Verificar o MKT de cada ponto de medição.
Com os resultados podemos definir, qual região é mais “perigosa” e realocar os materiais menos críticos para esta região. Se for o caso, a região deve ser interditada até que o problema seja solucionado.
Deve-se lembrar que deve ser anexado ao relatório final e ao protocolo de Qualificação o certificado de calibração de todos os loggers ou sensores utilizados nos testes.
Mantendo o status de Validado
Os testes devem ser realizados sempre de forma periódica. A periodicidade é definida de empresa a empresa. É aconselhável que a mesma seja feita de forma anual. Caso existam sensores monitorando os pontos mais críticos, é aceitável espaçar os testes para 2 em 2 anos.
Deve–se lembrar que esta definição deve ser escrita em análise de riscos e deve ser justificado qualquer mudança de periodicidade.
Segue abaixo as ferramentas que são fundamentais para manter o sistema validado:
- Controle de Mudanças;
- Formulário de desvios;
- Plano de calibração dos sensores;
- Plano de manutenção preventiva do sistema HVAC do depósito
- Protocolo de qualificação periódica ou revalidação
Deve-se lembrar que o ciclo é sempre contínuo durante a vida de um depósito, e qualquer mudança significativa deve ser validada.
Referencias Bibliográficas:
Convenção Farmacológica dos Estados Unidos:
- Dispositivos de Monitoração USP (36) Capítulo 1079– Boas práticas de Envio e Armazenamento
- Dispositivos de Monitoração USP (36) Capítulo 1118– Tempo, Temperatura e Umidade